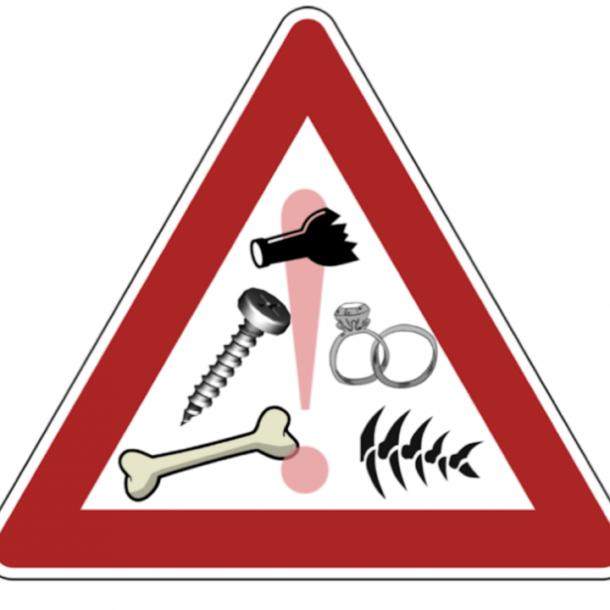
There is a new buzz among food packaging manufacturers: How to manage allergen(s) when shipping materials are sent back from manufacturers who facilitate declared allergens. Third party auditors are noticing return program of dunnage and are asking questions.
Let us share with you a true story. As a plastic bottle manufacturer, controlling allergens was as easy as requiring employees to wash hands after eating. Then one day, incoming inspection of returned empty boxes from a food manufacturer were coated with mustard smears. Suddenly, cross contamination of allergen was on our receiving dock! Now what do we do? And how do we manage those allergens?
Dunnage, corrugated cartons, trays, pallets and other shipping items are often sent back to the packaging manufacturer for reuse. This return program is viewed as cost saving and good for the environment. It is estimated that return packaging may grow from <5% to approximately 20% in the near future.
Influencing factors such as negative environmental impact issues are not expected to diminish significantly anytime soon and several governments are developing politics to promote global circular economy; it is expected an increasing number of potential situations where materials are reused and allergen cross contamination may occur (as was not predicted in the past).
How to address?
Before packaging manufacturers accept returnable packaging, it must be considered if this practice can introduce allergens into their facilities. For that, the best option is to require clients to provide declared allergen list with steps to control said allergens followed by visiting client’s facilities, understand their processes and look closely at the flow patterns of the packaging that will be returned. This means that not only the packing itself (after being used) and the place of storage should be monitored but also where the packaging flows inside the client’s facilities and which food products it may be in contact with. The first step is to work closely with the client to prevent or minimize contamination of the returnable packaging with allergens. For that, it should be considered to examine client’s risk assessment on allergens and/or even the packaging manufacture should perform its own allergen risk assessment at the client’s site.
Another important aspect: Is the packaging is washable? Can the clients cleanse the packaging with efficient processes? Checking these issues should be another point to include on the checklist when visiting the client. Certainly, when reusable plastic pallets are returned, this program should definitely be considered an option to eliminate the risk of returnable packaging carrying allergens back to manufacturer facilities.
In the case of unavoidable contamination by allergens, procedures must be put in place to validate if cleaning procedures (when applicable) are efficient in removing allergens or to verify if other control measures are achieving the intended results. For that the use of swab tests to detect the presence of allergens are a great option to consider.
Before we go in more detail, we would like to present a diagram that can be of guidance regarding how to manage this issue.