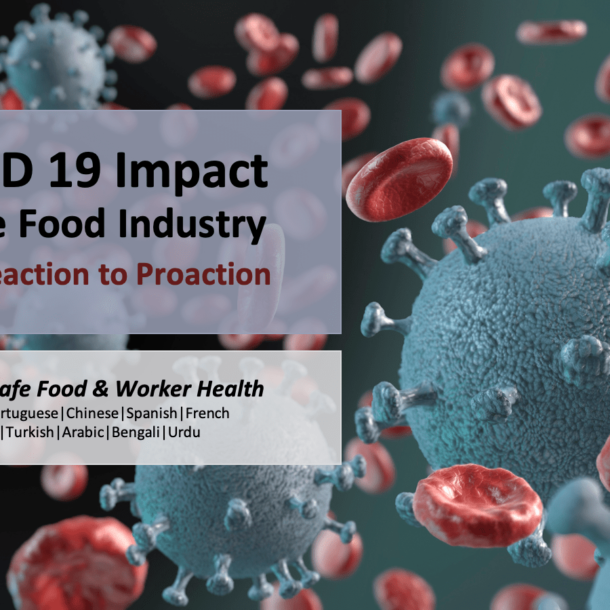
All over the world, food industry organizations closed their doors to non-workers as a way to stop the spread of the virus. Auditors were also left outside the door and 2nd party and 3rd party audits were simply postponed or canceled.
COVID-19 has impacted the food industry as no other event in history particularly because how fast and global were the consequences. Last month’s article was about the impact of COVID-19 in the food industry with a particular emphasis in changing from a reactive mindset to a proactive mindset. This month is a about a particular effect that was not addressed, audits.
All over the world, food industry organizations closed their doors to non-workers as a way to stop the spread of the virus. Auditors were also left outside the door and 2nd party and 3rd party audits were simply postponed or canceled. It is also known that inspections and controls from regulators and food safety authorities were also impacted, which increases even more apprehension with the level of control over food safety issues.
But this month the article is about the impact on audits. For this I invited 3 good friends to share their experiences and insights. They all are very experienced food safety professionals with decades on the road doing audits. There was no real guideline to their contribution. They just shared how they saw COVID-19 impacting audits and it is interesting to observe their different approaches on the topic.
Please share your own experiences in comments!
Enjoy the reading.