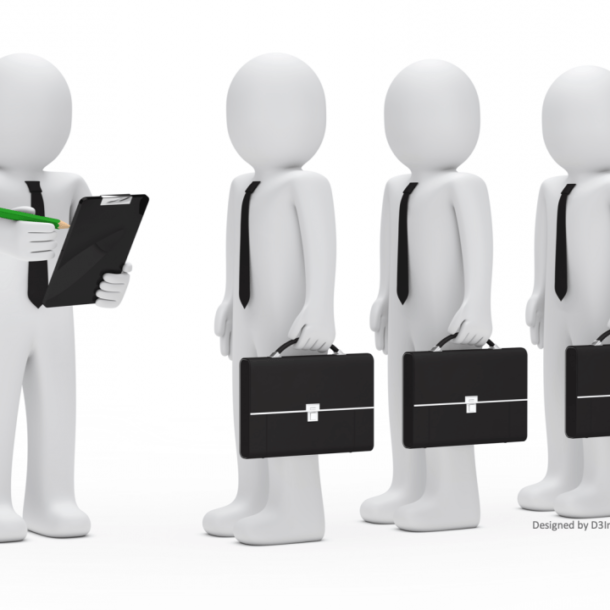
Audits or assessment is a question that we should deal with next time planning how to monitor suppliers.
We all know that auditing is far from perfect and some even question its efficacy in evaluating the adequacy of food safety systems. According ISO 19011 – Guidelines for auditing management systems (in 2018 update) audit is as systematic, independent, and documented process for obtaining objective evidence and evaluate it objectively to determine the extent to which the audit criteria are fulfilled. It is clear by this definition that the auditor should focus on obtaining objective evidence of compliance against a standard. And this is the very issue: the time and effort auditors have to devote seeking evidence to include in the report largely surpass the amount of time in questioning and understanding why the organization has chosen to do things as they do.
Time is in fact a key issue. Since time is money, most of the organizations are eager to get over the audit and get back to work, either because they do not see the benefits of audits or because they are undergoing too many of them (done by different organizations but following similar approaches and adopting similar requirements). Additionally, the longer the audit, the higher its cost.
All the above lead to a situation where check-list evidence are gathered as fast as possible, and everyone goes back to ”actual” work. But what is the actual gain in this situation? Is such a visit really effective?
Imagine you are a retailer interested in a product. A good price has been agreed upon but the only thing you know about the manufacturer is that it is certified. Is this enough to feel confident and buy or do you wish your consumers (and brand) be further protected? In most cases, another (wide scope) check-list based audit is planned. In fact, while an audit is essential for any certification process, an assessment would be a more effective tool to evaluate if and how a company achieves retailers’ key objectives.
What’s the difference?
Although not as wide ranging as the audit, an assessment displays a fresh look into things: while audits are intended to identify gaps against an established standard (for which compliance is the core purpose), assessments are more about understanding and learning a process, and the sustainability and adequacy of the food safety system to mitigate risks. Operations are analyzed in relation to the objectives instead of standard requirements. The system relies on the assessor experience, sensibility and knowledge of the client areas of attention. He tries to understand WHY people have chosen to do things the way they do and evaluate their suitability in achieving desirable outcomes.
Further, some standard requirements might not be relevant in some specific cases: what about external areas if your product is delivered in closed boxes or piped into the lines? Once standards required the use of blue plasters and pens also in blueberry processing plants! Who never addressed “applicable but unsuitable” requirements during auditing?
In assessing food manufacturing facilities, a system approach must be used. This means analyzing how the manufacturer identifies, characterizes and address hazards and risks. Auditors most commonly check if risk analysis is present and complete, assessors verify its adequacy to the threats and vulnerability of the product.
Reports have different approaches as well. In the audit report, cases of non-compliance are identified and classified in relation to a perfect score, while the assessment is focused on possible solutions and discussion about actions necessary to achieve key objectives; no score is present.
Which is better? Both of them!
They are different tools. The audit is based on verifying how well organizations define how to fulfil the audit criteria and if activities are done as stated or not. The assessor has no requirements or criteria and has to ask himself if the system of practices is effective or not. If an audit is essential for any certification process, an assessment is more effective to evaluate how a company achieves the key results. An assessment is not a proper tool for a certification. Third party audits need to stay the way they are as they check the compliance to a general standard shared among different operators (and auditors). In monitoring suppliers, integrating the assessment approach would mean being less generic and more focus on process and product specificities approach.
The best option for buyers is selecting certified suppliers and then assessing them for the effectiveness of their practices. In fact, a certification standard, having to ensure uniform and fair evaluation of performances, is a prescriptive document stating how things should be done in all areas. The auditor judges and attributes the weight of possible deviations on the basis of a check-list. Although, factories and foods are not all the same and a deviation can be crucial or have negligible impact depending on how processes are organized. Being able to rely on the work of certification auditor colleagues, the assessor can devote all due time to explore areas he considers essential to quality and safety of final products.
Sometimes manufacturer quality assurance department has to meet the standard although some requirements find no place in their risk assessment logic. This does not happen in assessments as a more flexible attitude is displayed, but procedures and activities must actually be effective to results (meaning high quality and safe food) rather than only being there, available to be shown.