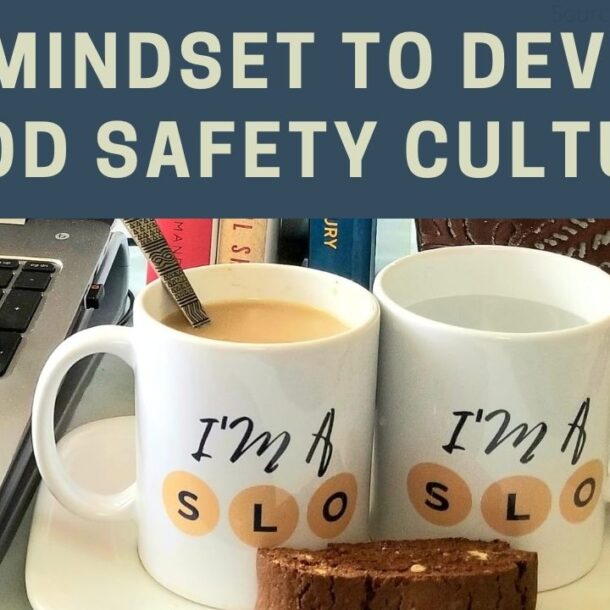
Digitalization is still not massively adopted and most of the time not because of lack of resources but to maintain the status quo.
Digitalization is still not massively adopted and most of the time not because of lack of resources but to maintain the status quo.
We live in a fast-paced world where technology has a core role. Most of us have in our pocket a powerful tool (cell phones) to be used to make our life easier and more productive. There are so many tools available that sometimes we feel we don’t have time to search for solutions that will save us time.
Digitalization is the conversion of text, images, and sound into digital form, via computer processing. This time-saving computer digital technology makes possible the instantaneous share-ability of text, images, and sounds with anyone in the world. Food Safety Systems (FSMS) are known as “too much paperwork” (and even some unnecessary bureaucracy). FSMS complexities are easily simplified if we address these basic questions to every document within it: 1. What is the purpose of this? 2. What do I get out of it? 3. Is this necessary to comply with a requirement?
Nevertheless, digitalization is a great solution to make everyone’s lives easier, especially to have faster access to information and insights about our food safety systems. Somehow it seems that this is still not massively adopted and most of the time not because of lack of resources but to maintain the status quo.
One of the things COVID-19 has taught us is that in managing crisis (like a pandemic), we need to use tools already available to keep the “wheels turning”. In addition, we ought to be trained and feel competent using these tools. Food Safety Professionals need to be able to do their jobs even for such work activities that arise outside of their offices. Digitalization, internet technology (IT) solutions, Cloud environment, Blockchain technology …. we need to embrace these tools to keep our food safe, assure high-quality food, and protect consumers.
When it comes to product recalls, digitalization provides various benefits.
In this article, however, we will focus on #1, #5, and #6:
Problem:
There are reasons why Food Safety Professionals, Store Managers, and Quality Team Members should not be sitting at their desks in an office. Staying home because of a pandemic is only one of them. Also, for example, caring for a sick or elderly family member or being on a business trip will keep them away from their regular office space.
Solution:
When you can conduct your daily work with the same level of expertise and professionalism while working remotely, this can make lives less stressful and less complicated. Existing technologies such as mobile phones, tablets, or laptops enable people to equally perform as if they were sitting at their desks in an office when, in fact, they are working from home or elsewhere.
Implementation:
In today’s environment, empowering employees by providing tools that improve their performance to their best potential ought to be provided. Mobile phones, tablets, laptops, and connectivity to a company server are the perfect support for remote working.
Problem:
Recall information needs to get to the right people at the right time in the right way. They need to know they can trust the information received. Today companies often use self-build, on-premise solutions – that only communicate internally – instead of cloud technology. When there is a recall, however, everyone along the supply chain needs to be informed. All recall related data needs to be transmitted fast with accuracy and reach the consumer on time.
Solution:
Cloud technology enables seamless global communication between companies and affected customers. Public recall information data is transmitted | communicated in a standardized, reliable way. Importantly, sensitive recall data is stored in a secure cloud account; response data of affected companies and the inbound-outbound activity data follow a specific designated path to an associated recall storage folder. Then in the future, this data is easily accessible for compliance, insurance, or reimbursement claim issues, etc.
Implementation:
Quality teams, management and IT need to work together to find suitable solutions for their needs. There are several providers out there with different approaches and offers. In most cases, IT companies with great expertise on the tech side lack recall knowledge. On the other hand, rarely are there service companies with great recall expertise that also have IT expertise included.
Problem:
The enormous amount of time Food Safety Professionals and Quality Team Members spend searching for folders and printed documents when ascertaining which products were contaminated and which customers received them is time-consuming, cost intensive, and overall, very ineffective.
With a product recall, time is of the essence.
Solution:
Storing all recall-related data online instead of physically in folders grants easy access and helps organize and manage processes. At the click of a mouse, locating necessary documents is easy. Specific reports can be either printed or shared online with third party auditors or insurance companies. Presenting proof for an insurance claim, starting a reimbursement process, or demonstrating compliance becomes as easy as that.
Implementation:
CRM, ERP, and document sharing systems help manage and organize company data not necessarily printed on paper and stored in a folder online. There is easy internal access to the data and the possibility to share information. Colleagues can work on the same document while sharing thoughts and comments on each other’s editing. Since there are plenty of options available for those needs, IT teams should always be part of the decision-making process. In the end they are the ones who will have to implement or set up whatever solution has been decided upon. Try signing up for free offers: CRM, ERP and document sharing solutions. Depending on each company’s needs and requirements, these could very well be a perfect fit – at least to start.
We wouldn’t finish this article without talking briefly about Blockchain solutions. These are great tools for track and trace – regarding products as well as affected customers. There are several solutions on the market to consider according to individual needs. However, because of the flexibility needed, the sensitivity of data, and the entire recall process itself, using Blockchain solutions to conduct a real-life product recall will not work. In order to get the best out of both tools – a Blockchain solution and a recall service – they would need to be combined.
First, collect all information needed from a Blockchain solution and then put that information into a recall system for fast and easy communication.
Currently, the biggest hurdle for combinations like that is the interoperability of both services. However, once that gets figured out, it will be a huge step forward in protecting consumers.
In our fast-paced world, food safety management must not be frozen in time (stuck in a paper-based status quo). Digitalization has proven to be a necessary tool that helps food safety professionals on their busy days … making it easier to gain access, share information, analyze, and act on food safety systems situations.
When it comes to recalls, every minute counts. Therefore, digitalization is extremely useful. Efficiently (faster and easier) recalling | withdrawing | removing contaminated food from the supply chain is essential to protect consumers from unsafe food and foodborne illness.
This article was written with Stephanie Weinand
Stephanie Weinand works as Global Development Manager for Recall InfoLink Inc., a company based in Boise, Idaho, USA. Recall InfoLink has developed a software solution for processing product recalls which is being used globally. She is a member of DLG, dti Deutsches Tiefkühlinstitut, ENFIT and IAFP. She is also connected to various representatives of international food authorities as well as other experts of the food industry. Stephanie has ongoing conversations with certifiers, auditors, consultants and lawyers. Next to building an international standard for processing product recalls, Stephanie is asked to do presentations at industry specific conferences, seminars and events. She is an author of technical articles and has also launched an interview “Industry Insights – connecting Experts to Experts”.
Disclaimer: The information contained on this article is based on research done in the last months and the authors personal experience and opinion. It is not intended to represent the view of any organization they work for or collaborate with. The authors will not be held liable for the use or misuse of the information provided in the article.